Staying safe at work used to mean not slipping on a wet floor or remembering to put on a hard hat. These days, it’s a whole different story. As jobs have become more complex, especially in construction, chemical handling, and tech-heavy fields, the ways we think about protection on the job have also changed.
What used to be a few basic rules written on a bulletin board has turned into full-scale digital systems, real-time alerts, and government-certified courses that walk people through what to do when things go south. But here’s the thing—people still get hurt. Accidents still happen.
And when they do, it usually isn’t because someone didn’t care. It’s because the systems in place weren’t clear, or people didn’t have the right training. The shift from simple safety rules to today’s layered approach has helped, but it’s also left a lot of people unsure about what they really need to stay protected on the job.
That’s where some surprising changes are taking root, and not just in labs or oil fields—but in how we talk about risk in everyday workplaces. Not all jobs come with hard hats and steel-toe boots. But that doesn’t mean safety doesn’t matter.
In fact, some of the biggest shifts in workplace safety aren’t happening in factories—they’re happening in hospitals, warehouses, schools, and even behind desks in corporate towers. With the rise of digital tools and cloud-based communication, a big chunk of what keeps people protected now happens behind the scenes. Still, physical danger hasn’t gone away.
Construction jobs are booming across the country, and the use of chemicals, heavy machinery, and complicated equipment hasn’t slowed down. In fact, it’s only grown. But what’s changed is the expectation that safety can be built right into the job itself.
People are looking for smarter systems, not just more rules. That’s why companies have been investing in tech and workplace safety at the same time. It’s no longer enough to tell someone to “be careful.
” Now there are apps tracking their movement, sensors measuring air quality, and even wearable devices that alert coworkers if something goes wrong. But all of that tech means nothing if the people using it aren’t properly trained. And that’s where the biggest gap often shows up.
It’s not about buying new tools. It’s about teaching people how to use them, what warning signs to look for, and how to react when danger shows up. People don’t freeze in emergencies because they’re careless.
They freeze because they don’t know what to do next. That’s a fixable problem—but it takes a deeper look at how we prepare workers in the first place. You’d think loud alarms, flashing lights, or big machinery would be the main dangers in risky jobs.
But most of the time, the real trouble starts in quiet moments. It might be someone skipping a small step in a cleaning process, or another person guessing their way through a chemical label they half-remembered from orientation. It might be a missed inspection.
A tiny leak. A ladder with one loose screw. These small things don’t make the headlines.
But they’re what lead to injuries that change lives, cost jobs, or shut down entire departments. That’s why safety is less about dramatic moments and more about small, everyday choices made by tired people in real-world settings. And yes, fatigue is part of the danger.
Long shifts, rotating schedules, and tight deadlines all eat away at judgment. Combine that with confusing manuals or rushed training, and you’ve got a workplace that looks safe on paper—but feels like a ticking clock. Even the companies trying to do things right sometimes fall short, not because they don’t care, but because they underestimate how much their workers really understand.
Communication, especially in high-risk industries, can’t just be top-down. It has to be a two-way street. Employees need space to ask questions, call out concerns, and report problems without worrying about being labeled dramatic or difficult.
When safety is treated like a group effort—not a lecture—it actually works. There’s a specific kind of training that’s quietly become a game-changer for people working around hazardous waste, toxic materials, and emergency cleanups. It’s called HAZWOPER training , and while the name might sound like something out of a sci-fi movie, it’s one of the most powerful tools a worker can have.
This training isn’t just about chemicals and cleanups. It walks people through real-life scenarios. Explosions.
Spills. Contamination. But it also breaks down what to do before any of that ever happens.
It builds muscle memory, decision-making confidence, and a stronger sense of what’s actually dangerous versus what just looks scary. That kind of hands-on, situation-specific training makes all the difference when the stakes are high. For industries like construction, environmental response, or manufacturing, having a team trained through HAZWOPER isn’t just a bonus—it’s an expectation.
The training goes beyond rules and digs into practical, situational thinking. And when workers go through it, they don’t just feel safer—they work smarter. They move differently.
They speak up sooner. And that’s the kind of culture shift that stops bad outcomes before they start. One of the most interesting shifts happening right now is coming from the younger generation of workers entering high-risk jobs.
These aren’t people who grew up accepting danger as part of the deal. They ask questions. They expect transparency.
And they’re not afraid to walk away from a job that doesn’t take their well-being seriously. That mindset has started to influence how employers think about risk. Safety manuals are being rewritten in clearer, more human language.
Visuals are replacing long blocks of text. Training videos now feature real-life examples, not just dull diagrams. And perhaps most importantly, younger workers are asking to be involved in safety planning from the start—not just trained after the fact.
There’s still a long way to go. But it’s encouraging to see that culture change can come from the ground up, not just from executives or industry leaders. When new hires walk into a job expecting better communication and smarter safety, it pressures the entire team to raise the standard.
And that ripple effect has the power to change entire industries from within. It’s tempting to think that accidents are just part of working in risky jobs. But that’s an outdated way of thinking.
Smart training, clear communication , and respect for the people doing the hardest work can change outcomes. It already has, in places where safety isn’t treated like a chore—but like a living, breathing part of the work itself. Keeping people safe isn’t just about checking boxes.
It’s about listening to workers, preparing them well, and trusting them with the tools and training they need to handle the worst—before it ever happens. That’s how real change takes root. And it’s already started.
.
Business
Is Safety in Modern Jobs Getting Riskier or Smarter? A Surprising Look Inside the Industries That Keep America Running
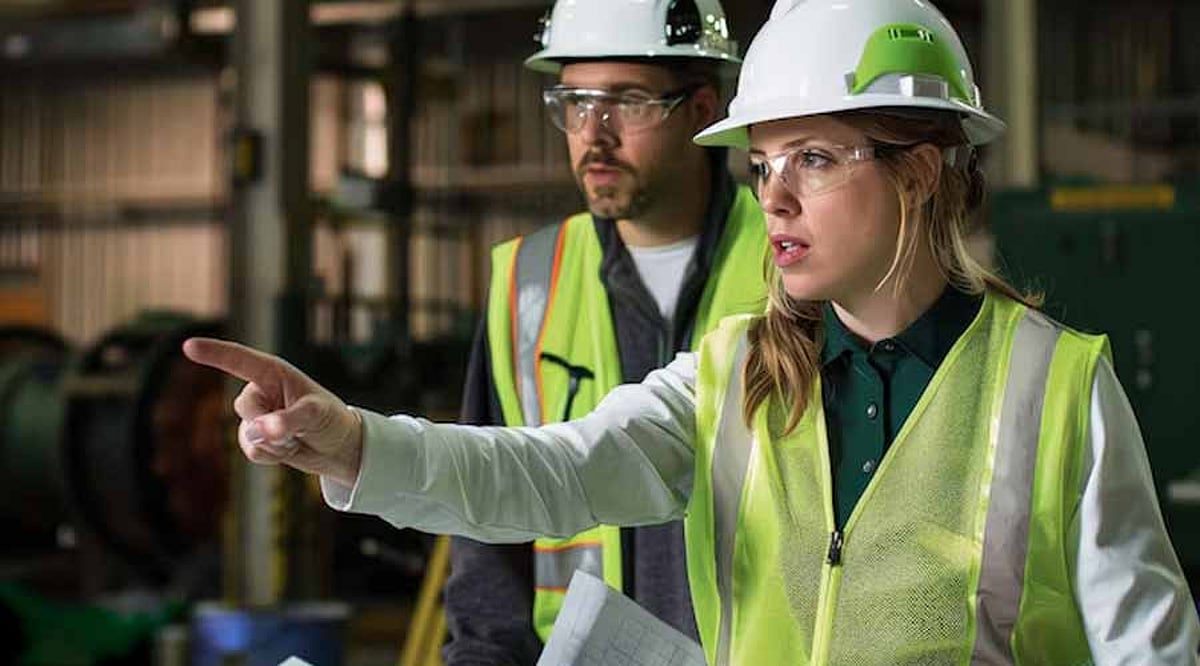